Continuous Mesh Belt Furnace (High-Temperature) by Therelek
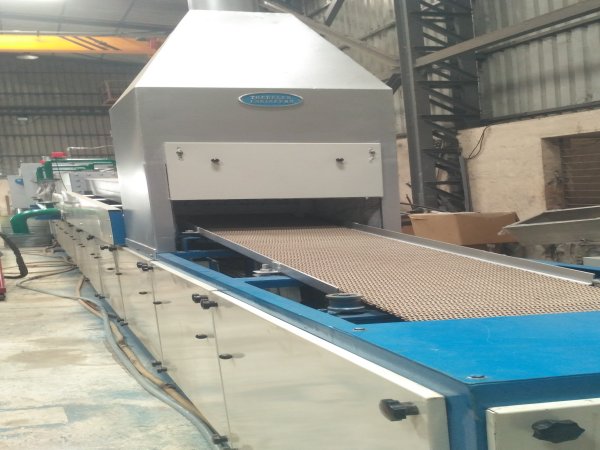
A multi-zone control environment is present in a continuous high-temperature furnace, often with a single pre-heating zone, followed by multiple heating zones and then cooling zones before exit.
Metallic muffles may be of stainless steel or high nickel and chromium-based alloys. Therelek offers plate belt furnace and conveyor chain furnace for conveying heavier jobs or components.
Features & Specifications
Temperature Range: Up to 800°C to 1150°C
Loading Options: Mesh belt, conveyor chain
Insulation: Vacuum Formed Ceramic Fibre Boards, Ceramic Fibre Blanket, Refractory Brick Lining
Heating Elements: Nichrome Wire/Special Alloy Resistance Heating Wire/Silicon Carbide
Instrumentation options: Thyristor, Programmable Temperature Controller, Temperature Recorder, PLC, SCADA, HMI
Additional Features: Muffle for Controlled Atmospheres of Nitrogen/Hydrogen/Cracked Ammonia/Argon
Gallery
Applications
Heat Treatment Applications
⇒ Hardening
⇒ Annealing / Annealing under protective atmosphere
⇒ Isothermal Annealing
⇒ Wire annealing
⇒ Normalizing
⇒ Case hardening
⇒ Decarb annealing
⇒ Blueing
⇒ Austempering / Bainitic hardening
Powder Metallurgy Applications
⇒ Sintering
⇒ Pre Sintering
⇒ Debinding/Delubing/Dewaxing
Other Applications
Controlled Atmospheric Brazing process is used in critical automotive applications because it ensures superior joint strength. Key aspects of brazing are
⇒ Filler Metal – most commonly an aluminum-silicon alloy that will flow quickly when melted and create strong joints post braze
⇒ Furnace – Inert/Controlled Atmosphere – retort and continuous (straight and humpback) furnaces
⇒ Flux – generally non-corrosive for aluminum applications; helps to reduce oxides on the metal surface which allows for filler metal to flow
⇒ Furnace Atmosphere, either:
- Nitrogen (N2) – displaces air/oxygen in the furnace atmosphere
- Inert gases – helium and argon; used in brazing metals and ceramics
Why Choose Therelek Engineers?
The answer is simple, Therelek is the best in the business when it comes to custom built furnaces and commercial heat treatment. Customer satisfaction is a guarantee at Therelek.
Through continuous innovation, we have achieved both consistent quality and an impressive clientele across the globe; some of them have been working with us for many years now.
What you avail from us is not just a product but a trustworthy and beneficial vehicle for your success. No matter what the size or sector of your company is, when you work with Therelek, you can be rest assured.
More about Continuous Mesh Belt Furnace
» Electrically heated
» Gas Fired
» Capable of achieving numerous metallurgical processes and can accommodate various heating types.
» Superior part to part temperature uniformity
» Increased throughput
» Process combination
» Lower upfront investment
» Reduced changeover times
» Part loading flexibility
- Types
- Advantages
» Electrically heated
» Gas Fired
» Capable of achieving numerous metallurgical processes and can accommodate various heating types.
» Superior part to part temperature uniformity
» Increased throughput
» Process combination
» Lower upfront investment
» Reduced changeover times
» Part loading flexibility
FAQs
Continuous furnaces are classified according to the number of heating zones, the method of moving the heated parts continuously through pre heating, soaking & cooling zones.
The temperature in continuous furnaces is constant over time and variable over the length of the furnace. In the heating and soaking zones the temperature is almost constant; in the holding zone it decreases toward the front of the furnace.