Stress Relieving Furnace Manufacturer in India
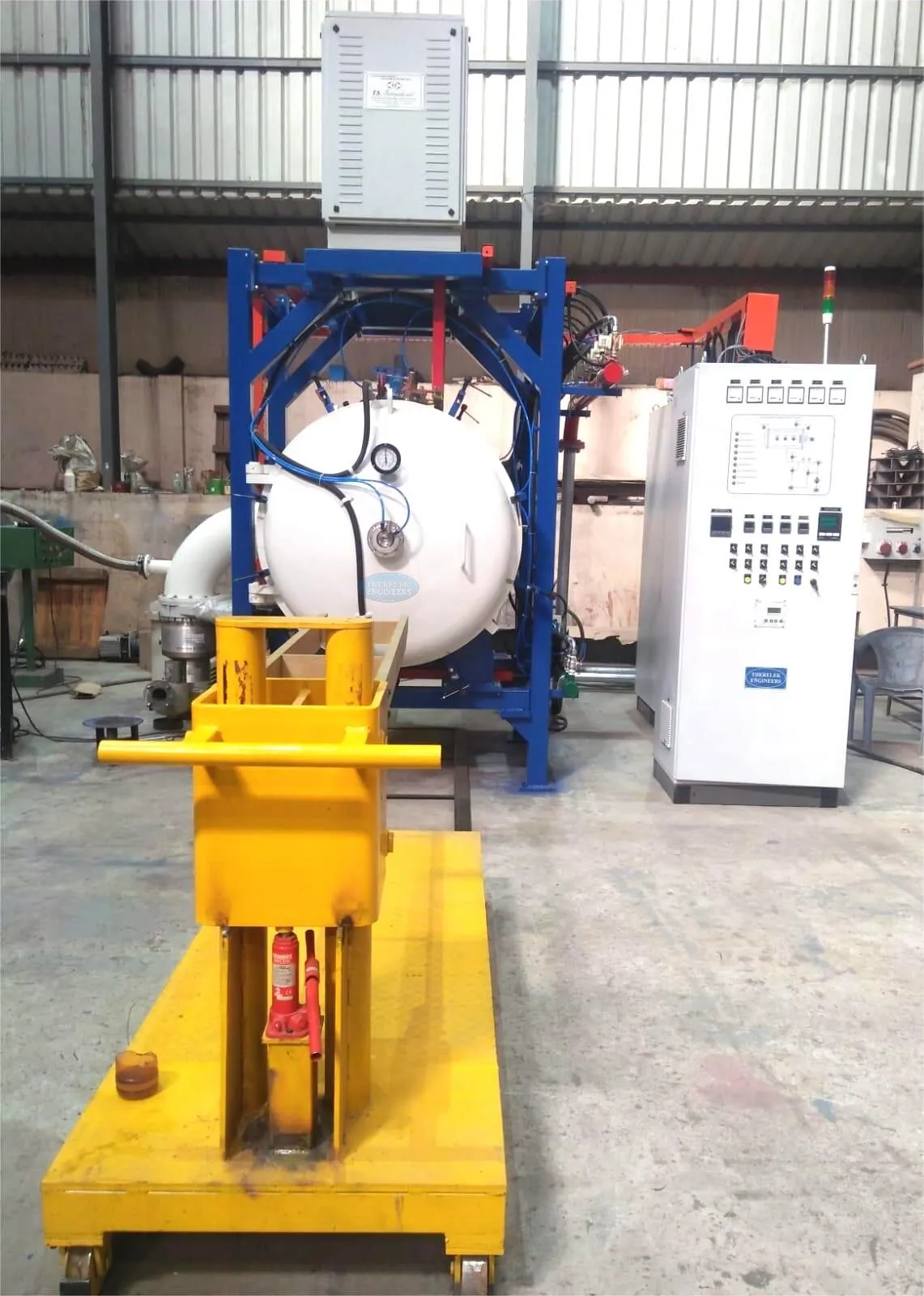
Stress Relieving Furnace Manufacturer in India
What is the Stress Relieving Process?
Stress relieving process is supposed to remove or reduce certain residual stresses induced in tools by heavy machining or while forming. Hence the probability of the tool getting distorted or cracked up during its hardening, gets reduced.
Stress relieving is a process involving relieving of internal stresses with no changes in the microstructures. The stresses in question are formed within the body due to grinding, surface hammering, cold working, case hardening, electroplated coatings, castings, welding, machining, precipitation and phase transformation are treated in this process.
The adverse effects with internal stress are when steel is under a residual stress and under a corrosive environment, it fails with stress corrosion cracking. Thus by enhancing the tendency of steel for warpage and dimensional instability. In the presence of residual tensile stress, the fatigue strength is reduced. Ductile materials are easily stress relieved when compared to brittle materials.
Ifs and buts of Stress Relieving Furnace
However, the ground surface of a hardened tool might get highly stressed post grinding but not really faulted. Again, the high stress on its part, might form fine cracks immediately post grinding, before or during use.
Ground tools with high residual stress can often be salvaged by stress relieving, immediately after grinding, at or just below the tempering temperature in order to maintain the specified tool hardness. Tools also develop high residual stress in use. It is sometimes advantageous to relieve this stress at each redressing of the tool by retempering, only at an appropriate tempering temperature; violating which would cause undesirable softening.
Some Fine Details on the checklist
Stress relieving is most commonly performed in air furnaces. Here, neither the heating nor the cooling rate is much crucial, although the cooling should be slow enough to prevent the introduction of any new stress.
Usually, protection against the scaling or decarburization is not that critical, unless the stress-relieving temperature is above 650 °C.
Post stress relieving, some corrections in certain dimensions might be required before hardening, as the relief of stress might end up causing some dimensional changes. Precision tools usually are stress relieved after machining and before hardening. It is often desirable to relieve stress after rough machining but before finishing machining.
Stress relieving after electrical discharge machining (EDM) work will reduce some of the residual stress but will not be able to remove all of the effects of this machining method.
Stress Relieving Furnaces by Therelek
Pit Type Low Temperature Furnace
Pit Type Low Temperature Furnace
Horizontal Vacuum Furnace
Horizontal Vacuum Furnace
Vertical Vacuum Furnace
Vertical Vacuum Furnace
Chamber Furnace
Chamber Furnace
Bogie Hearth Furnace
Bogie Hearth Furnace
Continuous Air Circulation Furnace
Continuous Air Circulation Furnace
Pyromaitre Ovens
Pyromaitre Ovens
Bell Jar Furnace
Bell Jar Furnace
Continuous Mesh Belt Furnace
Continuous Mesh Belt Furnace
Roller Hearth Furnace
Roller Hearth Furnace
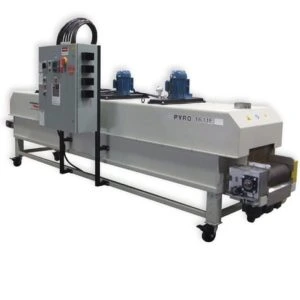
Low Temperature Pit Type Furnace
Pit type air circulation furnaces are installed with the opening at ground level or just above it. These are low-temperature furnaces with operating temperatures up to 650°C.